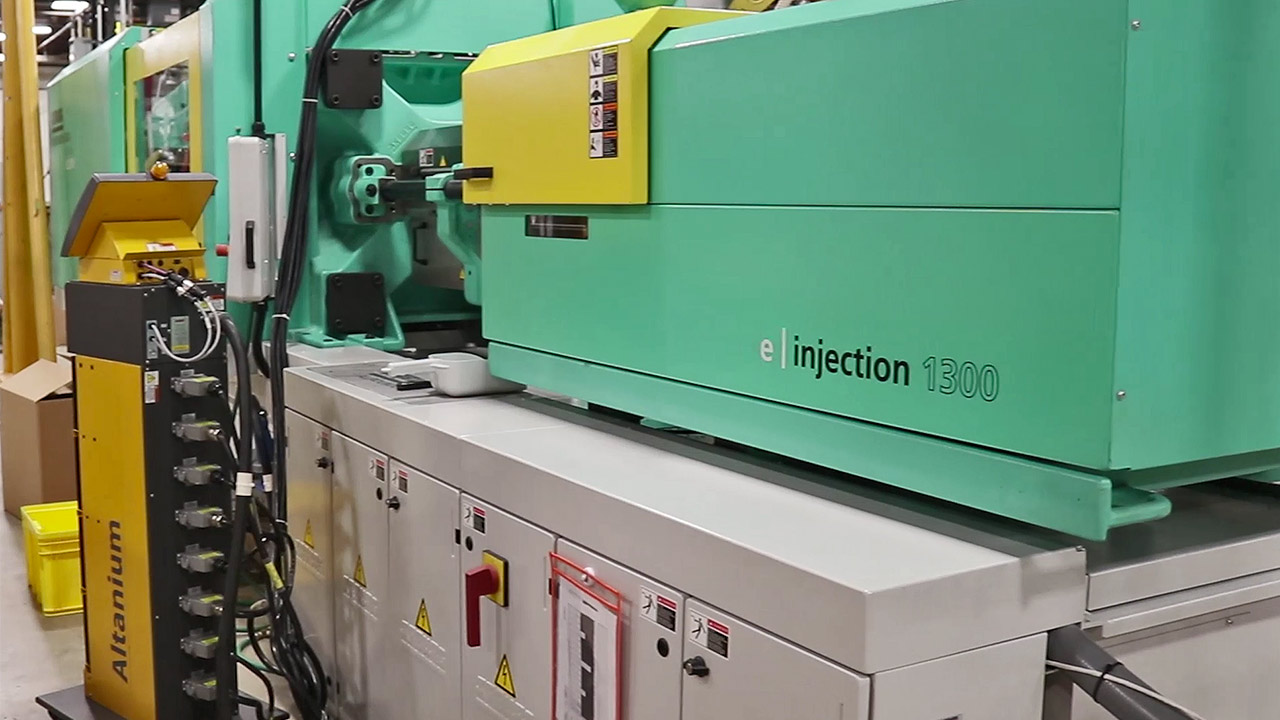
6. Set injection speed to 50% of customer’s machine, set holding speed to 5-10.
7. Set holding pressure to 0.
8. Increase the shot size gradually until parts are ~90% full. Check cavity variation. If more than 5% cavity variation, stop the trial and adjust.
9. Increase the shot size until parts are 100% full, parts can be sinky but not short. If parts have flash, burns or air traps, stop the trial and adjust.
10. Set shot size to 97% full.
11. Set holding pressure to ½ the actual injection pressure.
12. Start making gate freeze analysis and use holding time from where gate freezes.
13. Record weight of full shots.
14. Increase the holding pressure until part weight stop increasing.
15. Adjust cycle time to customer target. Make sure that tool can run properly at this cycle time.
16. Run off samples and mark them T1-X, quantity according to customer requirements if parts are ok. 1 balance shot and 2-3 runners should always be sent together with the samples.
1. Set barrel temperature according to recommendations from material supplier. Middle of recommended in front and lower of recommended in back. Record actual melt temp with air shot method.
2. Set mould temperature to middle of recommended temp span. Also make sure the actual mould temp is right during production.
3. Set clamping force according to Moldflow report, or max clamp of customer specified machine.
4. Set cooling time according to “time to reach ejection temperature” from moldflow report.
TIPTTOP Mould has taken injection molding to the next level by using scientific injection molding (SIM), which ensures the highest-quality product over a program's life cycle, regardless of molding machine, material or manufacturing location.
We use scientific injection molding techniques to develop process characterizations that guarantee repeatable molding, despite expected variation in materials and processing equipment. Injection molds are put through our rigorous statistical validation process to achieve the same critical molding parameters, regardless of manufacturing location or machine.
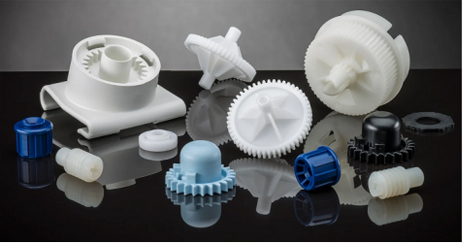